Students solve real-world problems with Charlotte-based company, alumni

Dr. Alan Turovlin’s undergraduate Supply Chain Management class works with Mark Harvey ‘05 and Corey Mabry to identify solutions for actual challenges faced by VS America.
On Tuesday, Sept. 20, Dr. Alan Turovlin welcomed CFO Mark Harvey ‘05 and Director of Operations Corey Mabry from VS America to present to his Operations 3208 (Supply Chain Management) class. This was more than a lecture from an alumnus and his colleague on how their supply chain works. Instead, it was a real-life example that can be used to demonstrate the concepts from the course.
“When Mark and Corey approached me about working with our students, I saw an opportunity to apply the concepts from class to a real company with real-world problems,” Dr. Turovlin said. “Mark, Corey and I structured a group project that would have students clarify the business need and design an improved supply chain distribution network. VS America presents challenges beyond just increased efficiency of their supply chain. They want to be responsive to customer needs and of course have products available — a big issue for almost everyone in today’s world — and now the students are right in the middle of solving one of the big problems facing companies today!”
Charlotte-based VS America is the U.S. operations of a 124 year-old privately owned German company. They specialize in ergonomic, adaptable and sustainable furniture solutions for K-12 schools, colleges and libraries with a line of over 2,000 unique, build-to-order products.
“As a UNC Charlotte alum, it’s been amazing to come back and participate on a project with this senior class and Dr. Turovlin,” Mark Harvey said. “This project resonates on so many levels for VS as we are a school furniture manufacturer working with K-12 schools, universities and libraries to ensure students have ergonomic furniture which is so necessary to their well-being. Bringing real-world logistic challenges to the senior class and hearing their engagement and excitement over the project has been really rewarding.”
VS America’s business practices present some unique challenges for the company — they ship customized and fully-assembled furniture from their factory in Germany, which means that the furniture cannot be produced in advance and stored as inventory. Additionally, schools make bulk furniture upgrades during a narrow three-month window each summer, creating huge peaks for the factory. Because these products are built to last a long-time, and school districts may place large orders, it might be 10, 20 or even 50 years before they place another order.
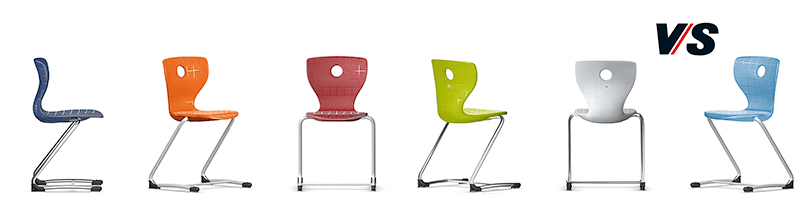
Over the next nine weeks, the students in Dr. Turovlin’s class will be given access to VS America’s data and research. Instead of traditional homework assignments, they will use the textbook and lectures to analyze VS America’s data. The project has the students create:
- A problem statement, focusing on the problems, concerns, and solutions sought by VS America.
- A distribution network utilizing VS America’s data by applying the processes and formulas from the textbook and class.
- Best practices for inventory and warehouse locations based on strategic direction to maximize customer satisfaction and corporate profit.
At the end of the project, the students will be able to compare their analysis with the actual actions that VS America took. With the majority of the class graduating in December or May, this assignment provides a valuable opportunity to sharpen their real-world problem solving skills before entering the job market.