Real-world recommendations from Belk College students
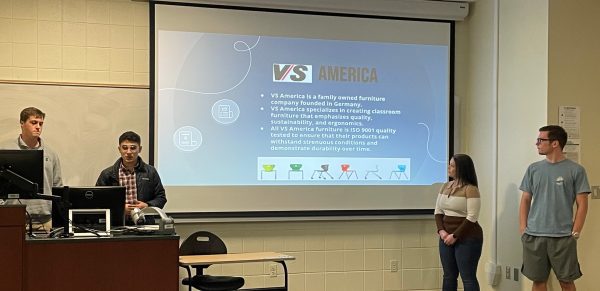
After nine weeks of research and analysis, Dr. Turovlin’s undergraduate students deliver their reports on how they would address supply chain challenges.
Since late September, Dr. Alan Turovlin’s Supply Chain Management class has been diligently combing through data supplied by VS America to pinpoint the key challenges faced by the company. The opportunity to apply course concepts to a real-life situation came about when VS America CFO Mark Harvey ‘05 and Director of Operations Corey Mabry approached Dr. Turovlin. He immediately recognized this as a way to provide his class with experience formulating improvements for a business that has a unique set of constraints. VS America is the U.S. operations of a 124 year-old privately owned German company that specializes in ergonomic, adaptable and sustainable furniture solutions for K-12 schools, colleges and libraries. For more information on VS America and the background of this project, read Students solve real-world problems with Charlotte-based company, alumni.
As the semester come to a close, each group presented their recommendations for VS America. Dr. Turovlin was quick to point out that in the real-world there is no answer key, you never have all the data you want and the only way to truly know if your solution is correct is to implement it and observe the results. These facts became evident in the wide range of valid proposals delivered by the students.
- Currently, VS America has warehouse locations in Charlotte, NC and Houston, TX. A number of groups proposed that a third facility be added to both reduce shipping costs and increase customer satisfaction through more timely delivery. The recommended locations for these warehouses ranged from the Great Lakes to the West Coast. Strong arguments were made for each location based on numerous factors including proximity to key customer bases, transportation networks, the cost of land, and even potential shifts in demand brought on by COVID-19 related education relief packages.
- All VS America products are presently built in Germany and ship fully assembled. While “German Made” is an important part of the VS America brand, some of the groups suggested that the benefits of shifting assembly and even production to the United States would more than offset any lost equity. The main factors cited by these groups were significant shipping cost savings and the ability to service more customers.
- VS America has thousands of customization options for its products. While this can lead to high customer satisfaction by providing them with exactly what they want, a few groups challenged VS America to rethink the overall customer experience. They proposed that by reducing customization and holding more finished products in inventory, VS America could reduce costs and lead times, which would result in more and happier clients.
The students appreciated the value they gained from this project beyond a simple grade. “I have been teaching students how to use Alteryx and Tableau during the Fall 2022 semester, and I utilized those skills to build maps and graphs so that VS America can make their final decision accordingly. If a student or new graduate can combine their passion, knowledge, and program (e.g., Tableau) features, they develop and enhance themselves in new ways employers like to see. This supply chain project has allowed students to gain exposure to problems that companies experience worldwide and prepare to gain the required skills, so students are prepared to work in the future,” said Ryan Shah ‘24.
Dr. Turovlin was also happy with the results. He indicated that he learned something new from each group’s presentation, and he plans to work with VS America to expand and grow the scope of the project in future semesters.